How ISO Certification standards drive operational excellence ?
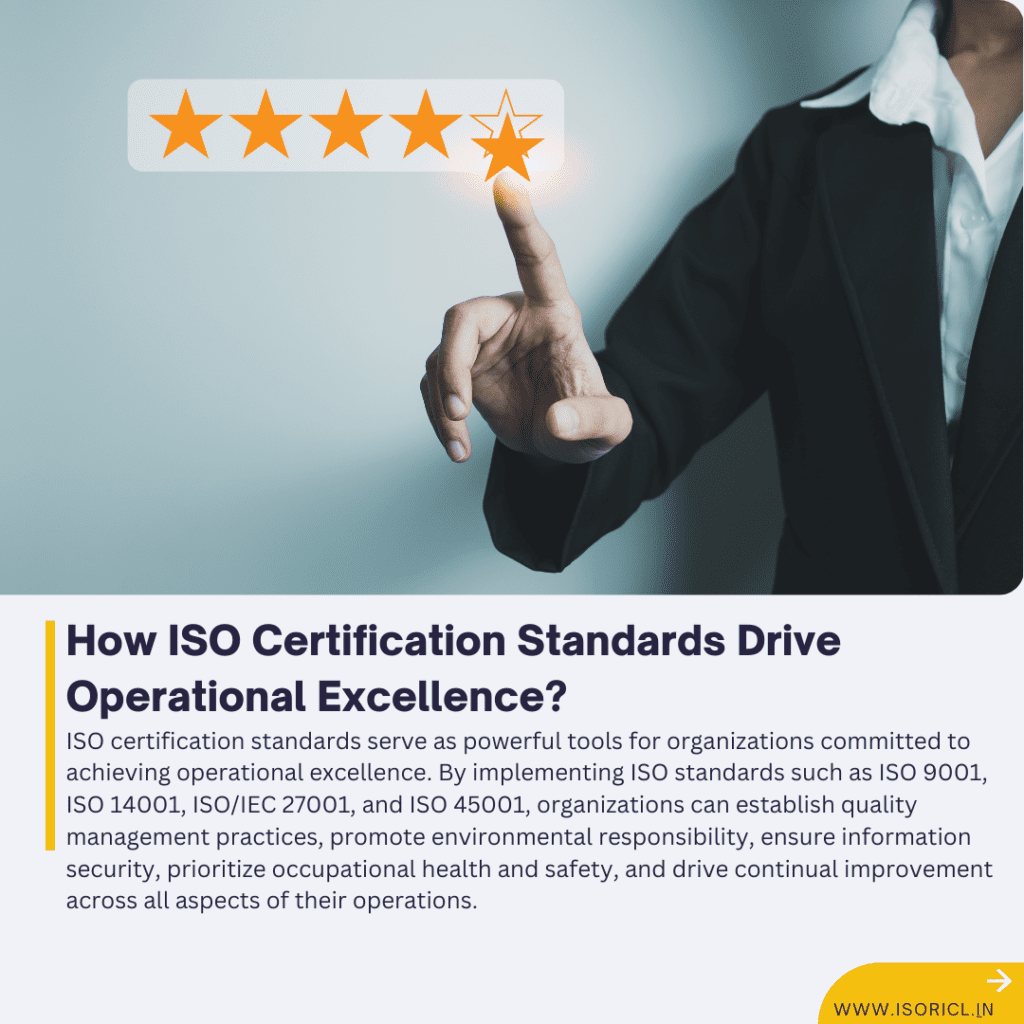
ISO certification standards play a pivotal role in driving operational excellence across organizations by establishing frameworks that emphasize efficiency, quality, and continual improvement. Here’s how ISO certification standards contribute to operational excellence:
1. Structured Processes and Documentation
ISO standards, such as ISO 9001 for Quality Management Systems (QMS), require organizations to document their processes and procedures. This structured approach ensures consistency and clarity in how tasks are performed, leading to:
Standardization: Standardized processes reduce variability and minimize errors, ensuring that products and services meet quality standards consistently.
Efficiency: Clearly defined processes streamline operations, reduce waste, and optimize resource utilization, contributing to operational efficiency.
Compliance: Documentation helps organizations comply with regulatory requirements and industry standards, avoiding non-conformities and associated penalties.
2. Focus on Customer Satisfaction
ISO standards, including ISO 9001, emphasize customer satisfaction as a core objective of operational excellence. By understanding and meeting customer needs, organizations achieve:
Improved Customer Relationships: Consistently delivering high-quality products and services enhances customer trust and loyalty.
Feedback and Improvement: ISO standards require organizations to gather customer feedback and use it to drive continual improvement. This customer-centric approach ensures that products and services align with market demands and expectations.
3. Continuous Improvement Culture
ISO certification fosters a culture of continual improvement, where organizations strive to enhance processes, products, and services over time. This culture is supported by:
Management Commitment: Top management’s involvement in setting quality objectives and promoting improvement initiatives.
Employee Involvement: Engaging employees at all levels in identifying opportunities for improvement and implementing changes.
Performance Monitoring: Regularly measuring and monitoring key performance indicators (KPIs) to track progress and identify areas needing attention.
4. Risk Management and Prevention
ISO standards, such as ISO 31000 for Risk Management, help organizations identify, assess, and mitigate risks that could impact operations. This proactive approach to risk management involves:
Risk Assessment: Systematic evaluation of internal and external risks, including operational, financial, and strategic risks.
Risk Mitigation: Developing strategies and controls to minimize the likelihood and impact of identified risks.
Business Continuity Planning: Establishing plans to ensure continuity of critical operations during disruptions or emergencies, thereby safeguarding operational resilience.
5. Employee Competence and Engagement
ISO standards emphasize the importance of competent and engaged employees in achieving operational excellence. This is facilitated through:
Training and Development: Providing employees with the necessary skills and knowledge to perform their roles effectively and contribute to organizational goals.
Empowerment: Empowering employees to take ownership of their work and participate in decision-making processes related to quality and improvement.
Recognition and Reward: Acknowledging and rewarding employees for their contributions to achieving quality objectives and driving improvement initiatives.
6. Data-Driven Decision Making
ISO standards promote data-driven decision-making by requiring organizations to collect, analyze, and utilize data effectively. This includes:
Performance Measurement: Establishing metrics and benchmarks to assess performance against objectives and targets.
Root Cause Analysis: Using data analysis techniques to identify underlying causes of issues or non-conformities and implementing corrective actions.
Continuous Feedback Loop: Iteratively improving processes based on data insights and feedback from internal audits, customer feedback, and other sources.
7. Supplier Relationships and Supply Chain Management
ISO standards encourage organizations to establish strong relationships with suppliers and manage their supply chains effectively. This includes:
Supplier Evaluation: Assessing suppliers based on quality, reliability, and adherence to standards to ensure consistent product and service delivery.
Supply Chain Resilience: Developing strategies to mitigate supply chain risks and disruptions, ensuring continuity of materials and services.
Conclusion
ISO certification standards drive operational excellence by promoting structured processes, customer focus, continual improvement, risk management, employee engagement, data-driven decision-making, and effective supply chain management. By adhering to these standards, organizations not only enhance their operational efficiency and quality but also strengthen their competitive position, build customer trust, and achieve sustainable growth. ISO certification serves as a blueprint for organizations to achieve and maintain excellence in their operations, adapting to changing market dynamics and driving long-term success.
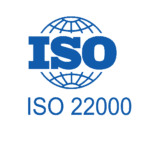
ISO 22000
Food Safety Management System
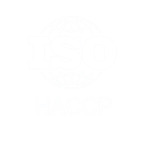
HACCP
Hazard Analysis and Critical Control Points
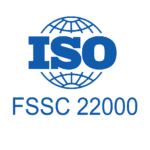
FSSC 22000
Food Safety Management Certification Scheme
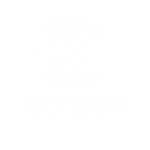
ISO 22301
Business Continuity Management Systems
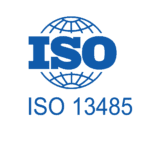
ISO 13485
Quality Management For Medical Device
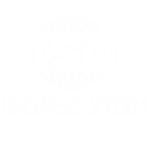
ISO/IEC 27001
Information Security Management System
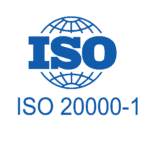
ISO 20000-1
Information Technology Service Management
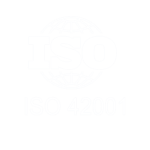
ISO 42001
Artificial Intelligence Management System
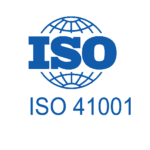
ISO 41001
Facility Management System
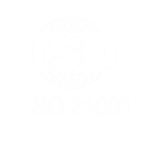
ISO 21001
Educational Organizations Management System
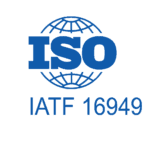
IATF 16949
Quality Management For Automotive
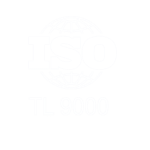
TL 9000
Quality Management System for Telecom
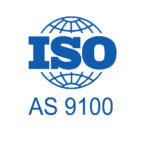
AS 9100
Quality Management for Aerospace Industry
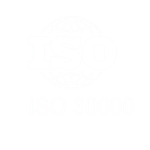
ISO 30000
Ship Recycling Management System
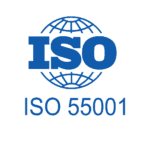
ISO 55001
Asset Management System