How ISO Certification strategy works?

Implementing an ISO certification strategy is a comprehensive process that requires careful planning, commitment, and execution. It involves understanding the ISO standards relevant to your organization, preparing your systems and processes, and undergoing a thorough assessment to achieve certification. Here’s a detailed guide on how an ISO certification strategy works:
- Initial Assessment and Planning
Understanding ISO Standards
The first step is to understand the specific ISO standards that are relevant to your industry and organization. Common standards include:
- ISO 9001 (Quality Management Systems)
- ISO 14001 (Environmental Management Systems)
- ISO 27001 (Information Security Management Systems)
- ISO 45001 (Occupational Health and Safety Management Systems)
Each standard has specific requirements that need to be met. Familiarize yourself with these requirements to understand what is expected.
Gap Analysis
Conduct a gap analysis to assess your current processes, systems, and practices against the requirements of the chosen ISO standard. This helps identify areas that need improvement or changes to comply with the standard. The gap analysis typically involves:
- Reviewing existing documentation
- Evaluating current practices and processes
- Identifying non-conformities
Developing a Project Plan
Based on the gap analysis, develop a detailed project plan outlining the steps needed to achieve ISO certification. The plan should include:
- Objectives and goals
- Timeline and milestones
- Responsibilities and roles
- Resources required (financial, human, and technical)
- Implementation
Establishing a Management System
Develop and implement the management system required by the ISO standard. This includes creating and documenting policies, procedures, and processes that align with the standard’s requirements. Key components often include:
- Quality Manual: A document outlining the scope of the management system, including policies and objectives.
- Standard Operating Procedures (SOPs): Detailed instructions for performing specific tasks to ensure consistency and compliance.
- Records and Documentation: Maintaining records to provide evidence of compliance and performance.
Training and Awareness
Ensure that all employees are trained and aware of the ISO standards and their roles in the certification process. Training programs should cover:
- Understanding of the ISO standard
- Specific roles and responsibilities
- Procedures and processes
- Importance of compliance and continual improvement
Implementing Changes
Make the necessary changes identified in the gap analysis to align with the ISO standard. This may involve:
- Revising existing processes
- Implementing new procedures
- Updating documentation
- Enhancing resource management
- Internal Audits and Reviews
Conducting Internal Audits
Perform internal audits to assess the effectiveness of the implemented management system and its compliance with the ISO standard. Internal audits help identify areas for improvement and ensure that the system is functioning as intended. The process includes:
- Planning the audit (scope, objectives, and criteria)
- Conducting the audit (reviewing documents, interviewing employees, observing processes)
- Reporting findings (non-conformities, observations, and opportunities for improvement)
- Taking corrective actions (addressing non-conformities and preventing recurrence)
Management Review
Hold regular management review meetings to evaluate the performance of the management system. These reviews should focus on:
- Audit findings
- Feedback from employees and customers
- Progress towards objectives and goals
- Effectiveness of implemented changes
- Identifying opportunities for improvement
- Certification Audit
Selecting a Certification Body
Choose an accredited certification body to conduct the external certification audit. Ensure that the certification body is reputable and experienced in your industry.
Stage 1 Audit (Documentation Review)
The certification process typically begins with a Stage 1 audit, which involves a review of your management system documentation by the certification body. This audit ensures that your documentation meets the requirements of the ISO standard and that your organization is ready for the Stage 2 audit.
Stage 2 Audit (On-site Assessment)
The Stage 2 audit is an on-site assessment where the certification body evaluates the implementation and effectiveness of your management system. This involves:
- Reviewing documents and records
- Observing processes and practices
- Interviewing employees
- Identifying any non-conformities
- Achieving Certification
Addressing Non-Conformities
If any non-conformities are identified during the Stage 2 audit, you will need to address them by implementing corrective actions. The certification body will verify that these actions have been effectively implemented.
Certification Decision
Once all non-conformities have been addressed, the certification body will make a decision regarding certification. If successful, you will receive an ISO certificate, which is valid for a specified period (usually three years).
- Maintaining Certification
Surveillance Audits
ISO certification is not a one-time achievement; it requires ongoing maintenance and improvement. The certification body will conduct periodic surveillance audits (typically annually) to ensure continued compliance with the ISO standard.
Continual Improvement
Commit to continual improvement by regularly reviewing and enhancing your management system. This involves:
- Conducting regular internal audits
- Holding management review meetings
- Addressing non-conformities and implementing corrective actions
- Seeking opportunities to improve processes and performance
Conclusion
An effective ISO certification strategy involves a thorough understanding of the relevant ISO standards, careful planning, systematic implementation, rigorous internal audits, and ongoing maintenance. By following these steps, your organization can achieve and sustain ISO certification, demonstrating a commitment to quality, efficiency, and continual improvement. This not only enhances your reputation and competitive edge but also drives operational excellence and long-term success.
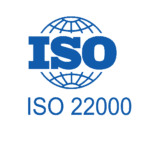
ISO 22000
Food Safety Management System
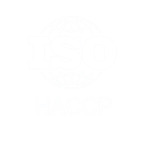
HACCP
Hazard Analysis and Critical Control Points
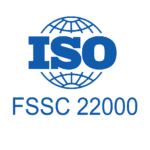
FSSC 22000
Food Safety Management Certification Scheme
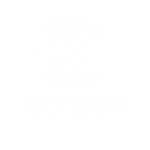
ISO 22301
Business Continuity Management Systems
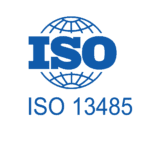
ISO 13485
Quality Management For Medical Device
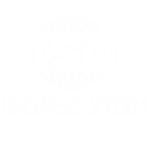
ISO/IEC 27001
Information Security Management System
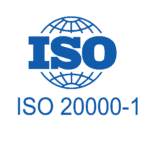
ISO 20000-1
Information Technology Service Management
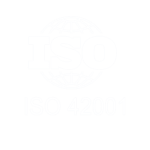
ISO 42001
Artificial Intelligence Management System
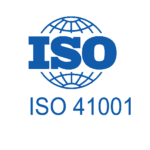
ISO 41001
Facility Management System
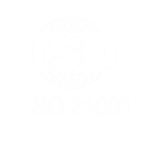
ISO 21001
Educational Organizations Management System
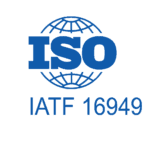
IATF 16949
Quality Management For Automotive
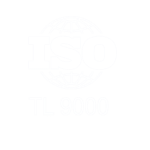
TL 9000
Quality Management System for Telecom
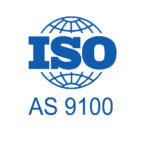
AS 9100
Quality Management for Aerospace Industry
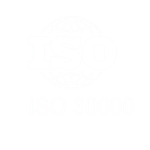
ISO 30000
Ship Recycling Management System
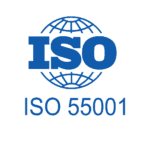
ISO 55001
Asset Management System